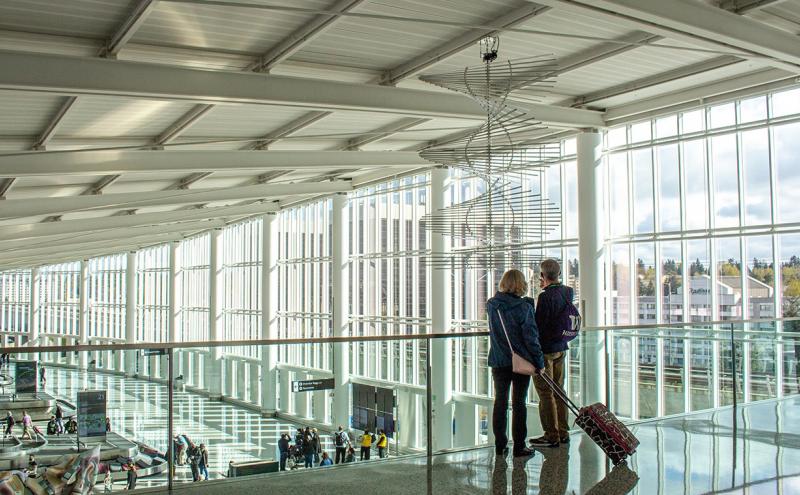
After a product is designed and manufactured, the final step is to verify the safety, quality, and functionality before you purchase it and use it in your everyday life. The newest features in your word processing software are run through a lifelike simulation before you use it to write your memoirs or your marketing plan. The vehicle you drive doesn’t leave the factory floor until it’s proven safe and functional. Verifying these last requirements is essential because the stakes for product failure can vary. If your paperclip fails, it’s not the end of the world. But if a vehicle — or a new building — has a safety defect or doesn’t meet the needs of the operation, the stakes and ramifications can be much more significant.
How do you verify that something as big as a building is ready for operation? Like a brand new 450,000 square foot building at Seattle-Tacoma International Airport (SEA)? Before the facility is open for use, it‘s extensively tested and trialed to ensure that it meets the needs of all stakeholders, including airlines, their providers, and government agencies. And (last but not least) you, the international jetsetter.
Here’s a behind-the-scenes look at how SEA verified the new International Arrivals Facility (IAF) — the most complex building project in the history of the airport — was ready to meet the needs of the operation and that staff and the building were up and running on Opening Day.
How does SEA use ORAT?
Many airports around the world use a similar process called Operational Readiness, Activation, and Transition (ORAT). This process includes familiarizing staff with new airport infrastructure and verifying that the new facility and systems are ready for operations. ORAT can scale from small to large building projects, and includes every facet of all systems inside the building, from baggage handling systems to podiums and queuing stanchions.
The ORAT discipline is relatively new at SEA and to a certain extent in the United States, but it has been employed in the Middle East and Europe for some time. At SEA, ORAT is not the same as testing and commissioning, which verifies that systems and equipment function as designed. ORAT goes a step beyond testing and commissioning into a function called Activation. This stage verifies that people working in the building know how to get to those systems, how to use them, and how to react to any issues. It also validates that the systems behave as expected under typical operating conditions. According to ORAT Senior Manager Charles Goedken, SEA uses ORAT to:
- Make sure staff are ready to operate in the new facility, and
- Ensure the facility is ready for operations
It’s critical to involve the ORAT team from the very start of a building project in the concept and design phases, as well as throughout the construction process. For the IAF, the ORAT team didn’t get started until well after design and part-way through construction, so there was a lot of catch-up, but they made it and the IAF is now open for operation!
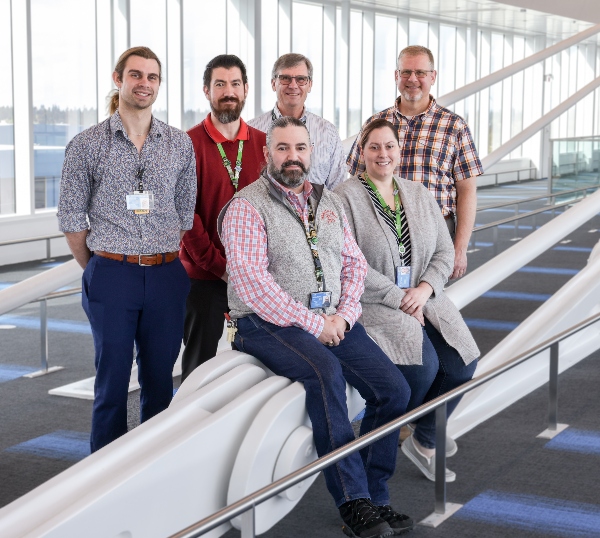
ORAT Process
The ORAT team provides feedback on how a facility is designed and can help catch operational design flaws or potential problems before the construction is complete and the facility is operational. For example, an architect might design a single elevator to serve multiple levels of a new building, but no nearby stairwell as a backup. The ORAT process is designed to catch those issues and here’s a linear overview of how it happens at Seattle-Tacoma International Airport (SEA).
PHASE 1: PLANNING AND DESIGN
When there is a need for a new facility at SEA, the process usually starts with developing a scope and concept of what the facility will look like and how it will be used. At this stage, ORAT is involved and develops the concept of operation. As the new facility is refined by the design team, ORAT reviews the design and contributes expertise in:
- Passenger flow
- Airport and airline operations
- How federal agencies function
- How the facility will be used by tenants, and
- Apply lessons learned from previous projects to improve the facility design.
ORAT starts to identify all of the stakeholders who will operate from the new facility or will be impacted by its construction and operation, to ensure they’re included and are operationally ready when it nears opening.
The real life process is less linear than the diagram above, so this diagram shows the complexity of designing, building, and testing a facility and how the ORAT process fits in.
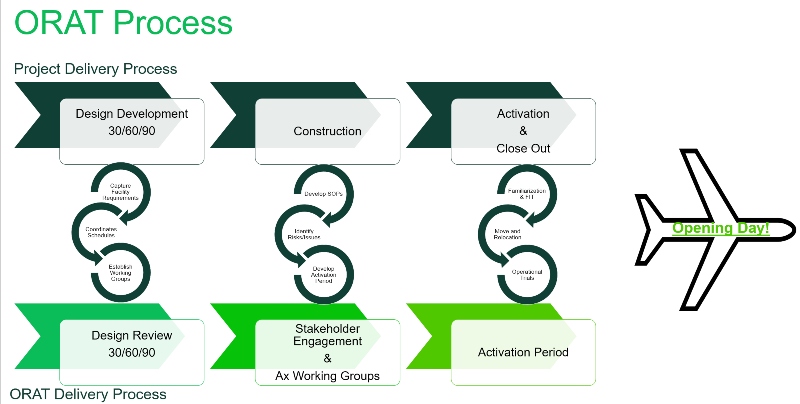
The main objectives in the Planning and Design phase are to:
- Ensure ORAT understands the new facility and is involved in developing the Concept of Operation
- Review and comment during 30/60/90% design reviews
- Engage all stakeholders at 60%, establishing Primary and Secondary Activation Representatives and regular Working Groups
- Establish the Governance Board and metrics for success
- Develop a project-specific Activation Plan
- Develop Standard Operating Procedures and Irregular Operating Procedures
Who needs to be involved?
In the case of the International Arrivals Facility (IAF), the stakeholders included tenants, as well as a multitude of entities that will use the facility or come in contact with the facility. Every one of those stakeholder groups had to be briefed and trained for their specific operation and workflow in and around the IAF.
- Aviation Stakeholders — more than 20 different airlines and their respective providers (ground handlers, wheelchair pushers, etc), as well as other providers for luggage carts, vending, custodial teams, artwork, and tenants from adjacent facilities that were affected
- Facility Tenants — federal government agencies like Customs and Border Protection (CBP), Transportation Security Administration (TSA), the Centers for Disease Control (CDC), and U.S. Fish and Wildlife (USFWS)
- Internal Port departments — the teams that keep the building and its systems up and running include Operations, Maintenance, Customer Experience, Information and Communication Technology, Facilities and Infrastructure, Aviation Properties (who maintain operating leases at airport), Air Service Development (who get new airlines to come to SEA), Pest Control, and many others
PHASE 2: CONSTRUCTION AND ACTIVATION
While the new facility is under construction, the ORAT team is refining the project-specific Activation Plan, a detailed plan to familiarize and train everyone working in the new facility. The Activation Plan also outlines the different Operational Trials that will be used to prove it is operationally ready. This stage requires a lot of contact with stakeholders to make sure they are fully in tune with the new facility, how their staff will operate in it, and what risks or issues may impact their operation. ORAT tracks all risks and issues to opening the new facility, working with the stakeholders to find appropriate mitigations or workarounds.
It usually isn’t until the very end of construction that tenants and frontline staff can go into the new facility. This time period is known as Activation, when all of the planning is executed. For some facilities Activation is easy, but the IAF was the most complex capital project in the history of this airport. Seemingly simple things, like getting to work in the IAF, were complicated and required lots of preparation and familiarization for each different group of employees. Another facet of Activation includes confirming Contingency plans for critical systems and operational processes, and ensuring that stakeholders are familiar and trained on them.
FIT (Familiarization, Introduction, and Training)
A new facility requires hundreds — if not thousands — of frontline staff who are familiar with working in a new space. New facilities typically include lots of new systems or equipment, which staff must become familiar with as well. For example, every group of stakeholders above needs to know:
- How passengers and airport employees enter and exit the facility
- Their organization's important areas of operations
- The existence and location of key passenger amenities (like pet relief stations, nursing rooms, new artwork)
- Key evacuation routes, safety equipment, and emergency procedures
- Details on the new equipment, Standard Operating Procedures, policies, and contingency plans
- Primary facility processes, like baggage systems or load docks
The end goal of this work is to provide an elevated experience for travelers. Goedken reinforces the importance of taking the time to focus on the detail.
“We do this work so we can become the gateway to the Pacific Northwest and the West Coast for airlines. It ensures that we offer a better experience to passengers by making sure all the tenants are prepared to work efficiently in the new environment.”
Operational Trials
Operational trials verify that new facility systems, equipment and processes work together to ensure the building will perform as needed for the operation. Trials also provide an opportunity for staff to be tested and demonstrate familiarity and training. This is a step beyond typical test and commissioning, which ensures new systems and equipment function properly. Baggage systems are tested with typical sized suitcases and luggage, but trials introduce baggage handlers, tugs and baggage carts, irregular shaped bags with loose straps, and staff who might not place bags on the belt properly, or space them out in an ideal way.
Testing and commissioning involves a third party hired by the Port to execute a carefully drafted plan. Operational trials include frontline staff who might be moving with a resounding sense of urgency as they drive into the baggage make-up area and throw bags on the belt haphazardly. ORAT develops each trial with the system or process owner to ensure objectives are clearly defined and measures of success are appropriate. The ORAT team is there to guide each trial and ensure it is recorded, documented and results are disseminated to the owner and participants so they know whether it passed or failed.
Standard testing for airports includes Gate Fit Checks, an advanced operational trial to ensure that gates are fully functional and ready for live operations. Each gate that is new or significantly modified undergoes a Gate Fit Check with an airplane (or two) to verify that each element, piece of gate equipment, and boarding and deplaning processes are ready for prime time.
Advanced Trials
Once the stakeholders and SEA staff are taught about the systems and the facility, the operational testing begins. This is essentially a “dress rehearsal” to verify that the facility and the staff are ready for prime time. This test uses stand ins for passengers and tests the facility operation and systems like HVAC, passenger flow, employee training, passenger loads, and new equipment.
The goal is to evaluate whether:
- All facilities, systems, and equipment are operationally ready
- Operating processes are defined and followed
- All staff know what they are supposed to be doing (and can do it) in the new environment
- Any areas of improvement are identified and fixed before the facility opens
Live Passenger-Flow Simulation
After construction is complete and before the facility opens to the public, one way to test a facility is a live simulation to test passenger flow and “stress” the system. In pre-pandemic days, the ORAT team would recruit around 1,500 participants from the community to use the facility and simulate the worst-case scenario of five or six planes deplaning at the same time. During the pandemic, the live simulations must be restricted to a couple hundred internal participants practicing social distancing and wearing protective gear.
It simulates the busiest midday arrival time with four or five international flights arriving at the same time. The testing process includes these tests (and many more):
- Bringing in passengers to walk through the facility and pick up bags
- Wheeling around the Smarte Cartes and making sure the planned routes and clearance work
- Pushing people in wheelchairs and walking with guide dogs to look for obstacles and test the accessibility of the facility
- Putting 200 people on the escalators to stress test the systems
- Loading 600 bags on the baggage carousel (a typical load for an arriving Emirates international flight)
- Looking for a drop in water pressure when people drink from two adjacent water fountains at the same time
- Verifying that all the soap dispensers are filled and the bathrooms have toilet paper
- “The Big Flush” — a trial where more than 40 Port employees use toilets, sinks, drinking fountains, and bottle fill stations at once to ensure water pressure and plumbing integrity and to mimic peak hour operations.
- Checking that there are changing tables in each of the nine family restrooms
- Testing the dedicated entrance and the way employees enter the building
- Simulating passenger flow inside the building and travelers entering and exiting the building
PHASE 3: TRANSITION AND OPENING
Transition plans should be developed early on, and dictate how and when a new facility will open. For the IAF, it was very much dependent on completion of construction and therefore the opening date was not set until the certificate of occupancy was issued. But once the date was set, everyone came together to complete their Activation activities, complete final planning of opening events, and make a great showing for this amazing facility.
This phase is usually very quick and fast-paced; all of the planning in advance helps to ensure the new facility and all the people working in it are ready for the Go/NoGo decision. For the IAF, the ORAT team had a Soft Opening Playbook that included flights, important IAF contact information, Activation and Opening milestone matrix, staffing plans, critical punchlist items that would affect opening, gate allocations, and facility maps. Progress was tracked through Soft Opening, a transition period of three weeks with limited live flights by completing up to three calls a day for planning and hot wash debriefs. These were streamlined as the process progressed and the teams ironed out operations; for example, the first debrief lasted an hour and half with all of the issues experienced from one flight, and the final debrief was less than 10 minutes.
ORAT coordinates overnight critical moves, as well as overseeing signage changes, opening day fresh cleaning, and closing off the old facility. To open a new facility, there are many behind the scenes changes like directories, online maps, website content, and SEA Underground subway changes.
PHASE 4: POST-OPENING SUPPORT
The facility and flow continues to be tested and optimized even after opening. Here, the question is asked “Does the initial plan for how to use this match how airport users are actually using the facility?” The ORAT team follows up with stakeholders and tenants on a daily basis to make sure new issues are addressed and resolved in a timely fashion. For instance, if a public address station stops working, does the staff know how to report that? Does it get fixed in a timely fashion?
ORAT also tracks outstanding issues that affect the operation. Per Goedken, there more things that need to get moved into the new facility after opening than there are before.
“We provide an opportunity for throwing things away called Dumpster Days — something that many people take for granted at work, but is necessary once you move out. The ORAT team continues to provide an important link between stakeholders and the Project Team during close-out, which is important when you are dealing with five different federal agencies and over 20 different airlines and all of their service providers.”
Last, but not least, we ensure the new facility tenants and operators continue to have a smooth transition and operation.
As Goedken likes to say, “their success is our success. If they are having problems, then ORAT is there to help solve them and make sure the facility, systems and new processes that have been carefully planned for years are indeed effective and functioning properly.”
What’s being activated at the IAF?
The short answer is everything — because it’s a brand new and very large facility. Goedken emphasizes the complexity of a holistic testing approach:
“The International Arrivals Facility has been the most complex capital project in the history of Seattle-Tacoma International Airport. So it makes sense that the ORAT process for this building is a monster. It involves landside operation, a new terminal, airfield trials, and alliances with five federal agencies and more than 20 airlines.“
IAF is ready for you!
The International Arrivals Facility is open for new operations starting today! And it’s not only beautiful and bright but operating efficiently and up and running for you. We can’t wait for you to see your new airport! Welcome here, Welcome home.